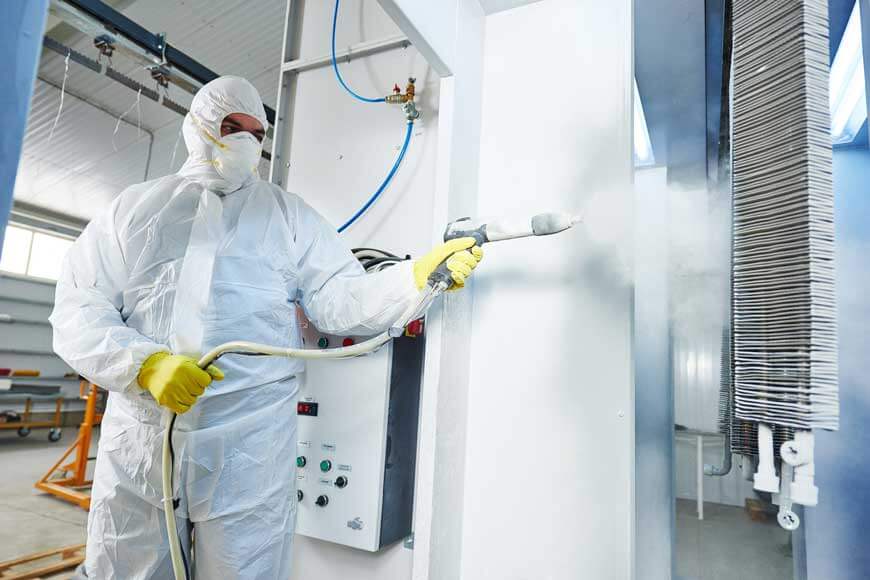
For the powder coating process, dry powder is shot through an electrostatic gun on to the metal exterior. The gun gives the powder a negative charge, and the negatively charged powder is attracted to the grounded part. The attraction results in fast, even application.
Once the coating reaches the desired thickness, the coated piece is placed in a curing oven, where the heated powder gels. Curing creates thermal bonds between powder particles, resulting in a smooth, hard finish.
Performance
A finish is meant to protect metal surfaces from corrosion and other environmental damage. If the finish is damaged by scratching or chipping, it ceases to function as an effective barrier.
Powder coating provides better performance than wet paint—it is more resistant to chipping, scratching, and other wear because of the thermal bonding it undergoes during curing, and because it can be applied in much thicker layers. This performance is especially important for outdoor products, like Aluminum Horizontal Fence and Aluminum Decks.
In addition to its physical toughness, powder coating provides superior color retention.
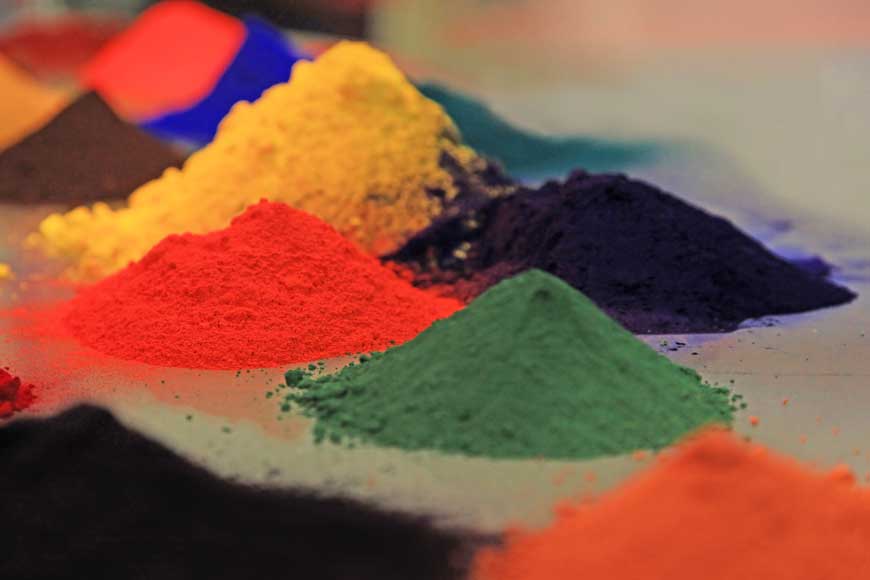
Health & Safety
Powder coating isn’t just more durable than liquid paint—it is also safer to store and apply.
Liquid paint is hazardous for several reasons. First of all, it’s flammable. Careless storage can easily lead to a dangerous chemical fire. Wet paint is also a health hazard to the operators that work with it.
Wet paint emits volatile organic compounds (VOCs). Long term exposure to VOCs, especially in enclosed spaces, causes respiratory irritation and compounding health problems. VOCs are also a major source of industrial pollution.
Because powder coatings don’t contain any fluids to evaporate, they don’t emit any VOCs, and are completely free of the associate health and safety risks.